Metal Stamping
An overview of metal stamping
Progressive Die Stamping is a very cost-effective way to produce a high volume of products. Raw sheet material in the form of coils is converted into a completed part by feeding it through multiple stations, each with a different station of the stamping tool. The material is always carefully measured to ensure that it has the proper thickness and width, before feeding it into the press.
In progressive die stamping, the coil is passed through a straightener, and then onto the feed that will push the sheet metal through the stations of the press. The strip of material then progresses from station to station, where it is shaped through notching, piercing, drawing, forming, and other operations as required by the design. Once this is finished, the completed part is cut off or blanked from the die and into a container.
Progressive die stamping has several advantages. This particular method of fabrication allows a single operator to perform the work of several with no part handling. And, once the strip is fed through the die, the press runs continuously until operations are complete.
Metal stamping at Regal
Regal Metal supplies parts to the automotive, truck, appliance and many other industries. We can either run tooling that we have designed and built, or we can run your existing tooling to your specifications.
The vast majority of the stampings produced at Regal Metal Products are completed through progressive die stamping; however, we perform secondary off-line operations when needed. To complement our press operations we also have in-house facilities for welding, bolt staking and assembly work. Regal also outsources production heat treating, plating, and painting, when these services are required.
Our production equipment
- Presses ranging in size from 250 ton to 600 ton
- Bed sizes ranging from 36″x60″ to 60″x168″
- Coil capabilities from .045″ to .312″ thick and up to 24″ wide
- Minster presses with Computerized Electronic Roll Feeders
- Equipped with Smart Pacs, Tonnage Monitors-Sesco Straighteners
- State-of-the-art AIDA servo motor presses
- (5) Dennison Multipresses with Six-station Rotary Tables
- (1) Continuous Welding Cell
- (2) Vibratory Deburring Machines
- (1) Tumbling Barrel
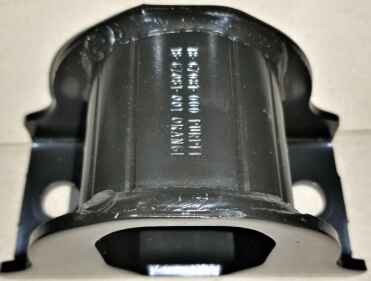
Ready to get started?
Don’t hesitate to contact us today! We are happy to assist you with any questions or requests that you may have.